Většina součástí vyráběných aditivní technologií vyžaduje určité dokončovací operace obráběním (tzv. post-processing) pro vytvoření požadované přesnosti a kvality povrchu. Obrábění může být náročné vzhledem ke komplexním tvarům nebo odlehčeným tenkostěnným konstrukcím. Tyto vlastnosti vedou k vibracím, které mají negativní dopad na celý proces a kromě vibrací existuje problém s ustavením, vyrovnáním a upnutím prototypu ve sklíčidle nebo svěráku.
Článek vychází z příspěvku (anglicky) Marca Saunderse, který v něm popisuje jak vyrobit odlehčené části dostatečně tuhé, aby mohly být efektivně obrobeny a navrhuje, jak provést ustavení součásti pro obrábění částí vytvořených aditivní technologií. Dále v příspěvku uvádí použití metrologické sondy pro správné zarovnání součástí.
Aditivní výroba umožňuje navrhnout a vyrobit součásti, které prostě nelze vyrobit jiným způsobem. Tato skutečnost přináší nesporné výhody v oblastech, jako jsou odlehčené struktury a tepelné účinnosti. Samotný proces je často plně automatizovaný a vysoce efektivní a navíc vše probíhá s minimální produkcí odpadu. Tyto přínosy jsou ovšem kompenzovány reálnými problémy s post-processingem, což může být velice obtížné odstranit, pokud zvolíme špatný přístup. Aditivní technologie zatím nedokáže vyrábět přesné výrobky, které vyžadují tolerance a vůle pro uložení, takže následné obrábění je nevyhnutelné. Podobné problémy řeší i výrobci kompozitních a superplastických dílů. Komplexní tvary způsobují zkroucení a vychýlení, které má dopad na konečnou přesnost. Producenti aditivních technologií se mohou od těchto výrobců poučit a aplikovat stejné postupy pro jejich případ.
Pokud součást vyrobená aditivní technologií vyžaduje obrábění, potýkáme se s řadou výzev. Před samotným obráběním musíme provést analýzu a zodpovědět si zásadní otázky.
- Je upnutí prototypu dostatečně tuhé, aby sneslo zatížení vznikající během obrábění?
- Bude součást odřezaná elektroerozivním obráběním nebo pilovým kotoučem?
- Je upínací zařízení dostatečně tuhé a flexibilní (předpokladem je víceosé obrábění)?
Odpovědi na tyto otázky demonstruje následující případová studie:
Vedení mikrovln
Případová studie řeší vedení mikrovln pro telekomunikační satelit. Kritickými faktory jsou váha vedení, účinnost přenášení mikrovln a velikost prostoru. Tato studie je dobrým příkladem lehké konstrukce a konsolidace jednotlivých dílů, která odstranila šrouby, což vede k efektivitě přenosu vln a snížení zpětných odrazů. Díky snížení počtu přírub a spojovacích šroubů se zmenšila celková váha dílce o polovinu a odpadl montážní proces. Tohle jsou všechno výhody aditivní technologie, ale součást stále potřebuje obrobit příruby na každém konci vedení.
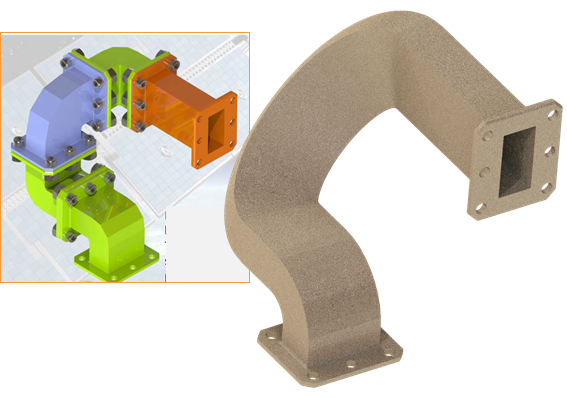
1. Stanovení řezných sil
Pro stanovení řezných sil se používá dynamometr. Veškeré obrábění bude probíhat v rovině XY s použitím procesní kapaliny. Naměřená data z dynamometru ukazují průběh zatížení při obrábění a lze pozorovat nejvyšší hodnotu zatížení. Ta vzniká při vstupu břitové destičky do oblasti řezu a je zhruba dvojnásobná než střední hodnota zatížení. Dále můžeme experimentovat s různými hloubkami řezu a pozorovat jejich ovlivnění.
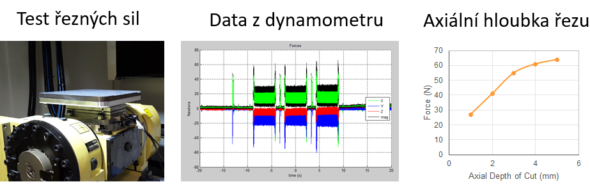
2. Simulace řezných sil
Zatížení řezných sil tedy už známe, je ale součást dostatečně tuhá aby toto zatížení vydržela? Pro ověření této skutečnosti provedeme pevnostní analýzu a aplikujeme na ní data naměřená z dynamometru. Prozatím budeme uvažovat ustavení v klasickém svěráku za podélnou část vedení. Metoda konečných prvků ukazuje, že obrábění kolem okraje příruby vede k významnému vychýlení a to více než 150 mikronů, což bude mít negativní dopad na přesnost a výsledný povrch součásti. Potřebujeme tedy zlepšit tuhost součásti během obrábění. Existují dvě možnosti:
- změna konstrukce,
- změna upnutí.
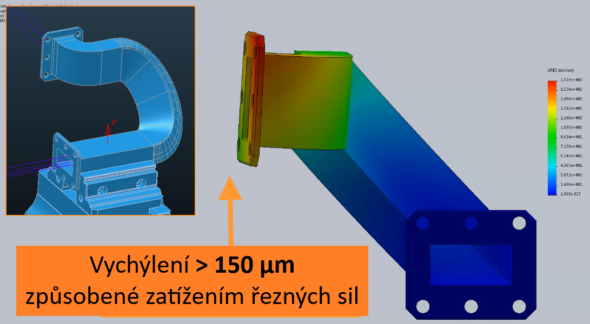
3. Změna/optimalizace konstrukce součásti
Jednou z možností jak zlepšit tuhost konstrukce je provést drobnou změnu v návrhu součásti. Jak lze vidět na obrázku níže, bylo přidáno několik úchytů, které spojují oba konce a tím se redukovalo vychýlení vznikající při obrábění. Redukce vychýlení je 50 %. Může být navržené mnohem sofistikovanější řešení úchytů, je ale nutné uvažovat o tom zda úchyty nezasahují do prostoru, kde bude něco jiného a jestli jsme stále schopni upnout součást do svěráku.
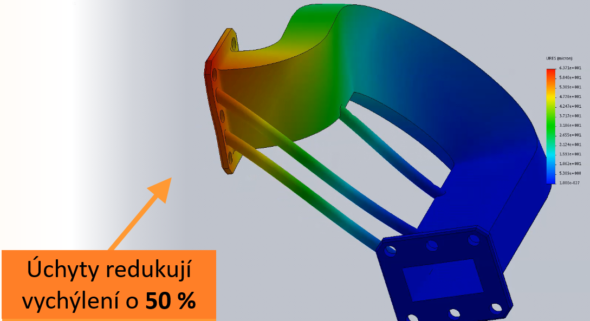
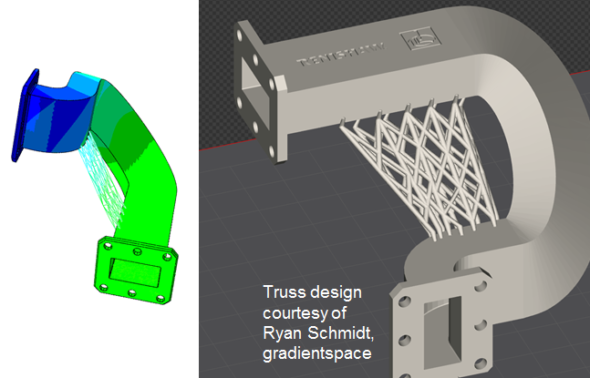
4. Upnutí
Pokud nelze jednoduše změnit návrh konstrukce součásti, aniž bychom ztratili výhody, které aditivní technologie přináší, musíme se podívat na jiné způsoby upínání. Potřebujeme najít způsob jak vytvořit podporu mezi oběma konci přírub k minimalizování vibrací a vychýlení. Dále nesmí dojít k poškození součásti při pevném sevření. Jako řešení můžeme zkombinovat pouzdro vytvořené z plastu pomocí aditivní technologie a takzvaných pinů. Díky tomu se rozloží upínací síla, což redukuje riziko vychýlení a vzniku vibrací.
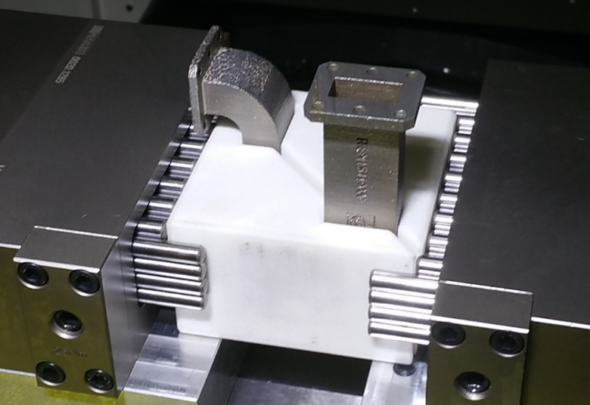
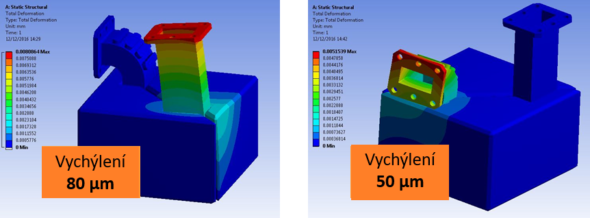
5. Obrábění
Je-li součást upnuta a upnutí je dostatečné tuhé, může se začít s dokončovacími operacemi. S výslednou přesností obrábění souvisí přesnost a tuhost soustavy stroj, nástroj, obrobek a přípravek, přesnost CNC obráběcího stroje. Přesnost výroby se ověří 3D měření nebo skenováním.
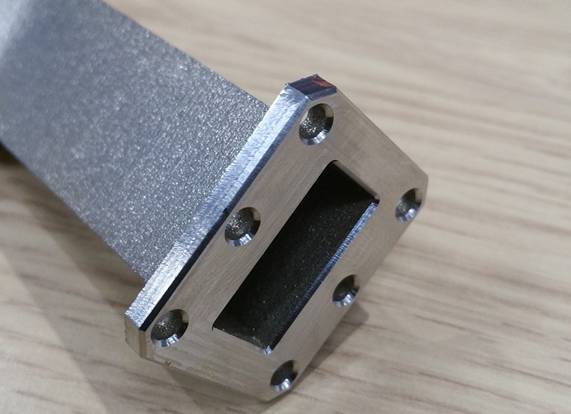
Přesné obrábění je často velmi důležitým prvkem v procesu aditivní výroby. Funkčně optimalizované součásti aditivní výroby nemusí být příliš tuhé a často potřebují složité přípravky. 3D vytištěná pouzdra (čelisti) mohou poskytovat v tomto případě dobré řešení.
Zdroj: Marc Saunders, You can build it, but can you finish it?