Technologie 3D tisku vnáší do výroby různorodých produktů zcela nové příležitosti, a to v mnoha ohledech. Nejinak tomu bylo v případě konstrukce rámu horského kola pro firmu Empire Cycles, kde se naplno projevily ohromné benefity moderních 3D technologií.
Chris Williams je nadšený motorkář, cyklista, ale taky designér a majitel firmy Empire Cycles, která ve Velké Británii vyrábí horská kola pro náročné zákazníky. Aby se prosadil ve značně tvrdé konkurenci na trhu jízdních kol, zaměřuje se na high-end ve spíše menších sériích kol, z nichž je patrná osobitost a taky to, že jejich tvůrci využívají někdy ne zrovna tradiční technologie.
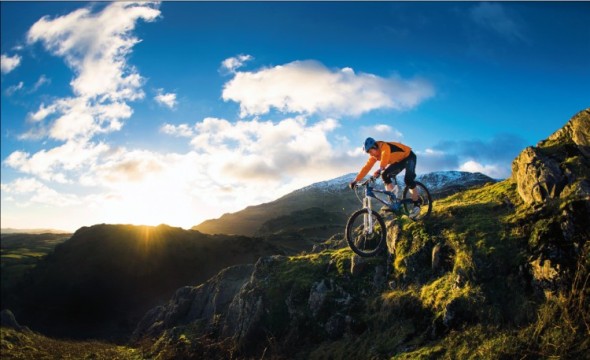
Ideu o vytvoření vlastní úspěšné série horských kol postavil Chris Williams na zkušenostech, jež si přinesl z motokrosu. „U motokrosových motorek se mi líbila kombinace jednoduchosti a pevnosti,“ říká, když popisuje, proč a jak tyto praktiky přenesl do světa cyklistů.
Touha o prosazení se mezi nejznámějšími dodavateli horských kol se mu vyplnila, když všechny ostatní předběhl vskutku unikátním projektem rámu, jenž byl jako vůbec první na světě vyroben z titanové slitiny metodou 3D tisku. Značka Empire Bikes se tak stala ikonickou nejen pro svůj název, ale pro technologický skok, jenž jí zajistil přítomnost v médiích po celém světě.
Slitina z titanového prášku
MX6-R označuje dosud jediný exemplář plně odpruženého sjezdového kola typu „enduro“, jehož nosné díly jsou vyrobeny z titanu a slepeny strukturálním epoxidovým lepidlem od 3M. Na počátku jeho vzniku byla mnohem skromnější myšlenka, spočívající v pouhé úpravě objímky sedla existujícího sportovního kola MX-6.
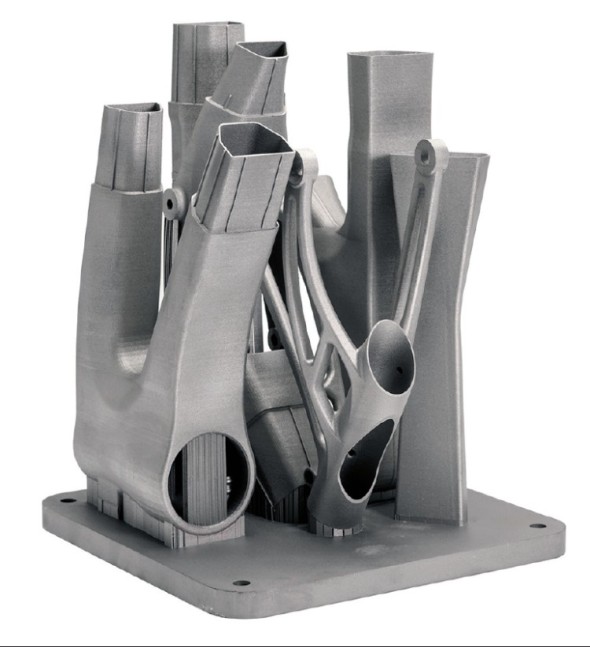
Jeho geometrie byla podrobena výpočtům tzv. topologické optimalizace, zajišťující ideální tvar výrobku vzhledem k jeho pevnostním vlastnostem. Výpočet metodou konečných prvků probíhá ve specializovaném softwaru v postupných iteracích, přičemž se z oblastí méně namáhaných odebírá materiál, dokud nevznikne konstrukce zcela optimalizovaná z hlediska nosnosti. Výsledný díl je pak díky nízkému objemu materiálu maximálně lehký a přitom pevný.
Vzhledem k tomu, že výsledná podoba takto zoptimalizovaných prvků často připomíná až anatomické tvary obtížně vyrobitelné konvenčními technologiemi, nachází právě při takových projektech ideální využití 3D tisk. V tomto případě, kdy hovoříme o využití profesionálního zařízení pro tisk kovových dílů či prototypů, je však přesnějším termínem aditivní výroba.
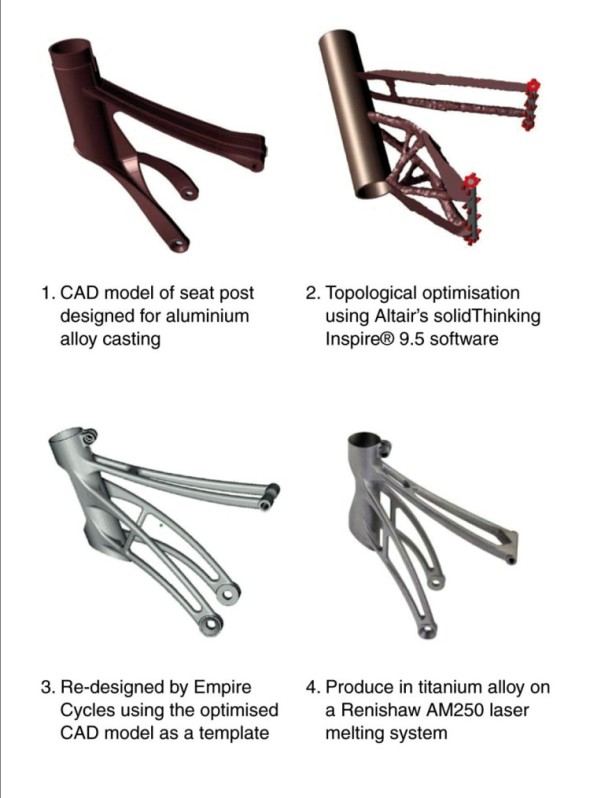
Optimalizovaná objímka sedla byla takto vyráběna ve spolupráci s britskou společností Renishaw na jejím zařízení AM250 metodou laserového spékání kovového prášku (SLM – Selective
Laser Melting) ve vakuové komoře vyplněné argonem. Tento stroj dokáže produkovat výrobky z nerezové oceli, hliníku, titanu, kobalt-chromu a inconelu, jež vznikají postupným tavením mikroskopických vrstev kovového prášku prostřednictvím laseru o průměru paprsku 70 mikrometrů s vertikálním rozlišením tloušťky vrstvy v rozmezí dvacet až sto mikrometrů. Maximální velikost výrobku je dána prostorem komory, který činí 250 × 250 × 300 milimetrů.
Extrémně pevný, ale lehký
Výsledek, který pracovníci Renishaw pro Empire Bikes poskytli, Chrise Williamse nadchnul a není se proč divit – vyrobený díl z titanu s optimalizovanou topologií byl o 44 procent lehčí než jeho hliníkový předobraz a zároveň ohromně pevný. Objímka sedlovky byla testována podle normy pro horská kola EN 14766, přičemž vydržela padesát tisíc cyklů síly 1200 N. Testování pokračovalo bez závady šestkrát déle, než je obvyklé.
Tyto impozantní parametry zaujaly všechny zúčastněné natolik, že přistoupili k rozšíření tohoto procesu na celý rám kola. Vzhledem k velikosti stavební komory 3D tiskárny bylo nutno konstrukci rámu rozdělit na jednotlivé části tak, aby bylo možno využít maximální stavební výšku 300 milimetrů stroje AM250.
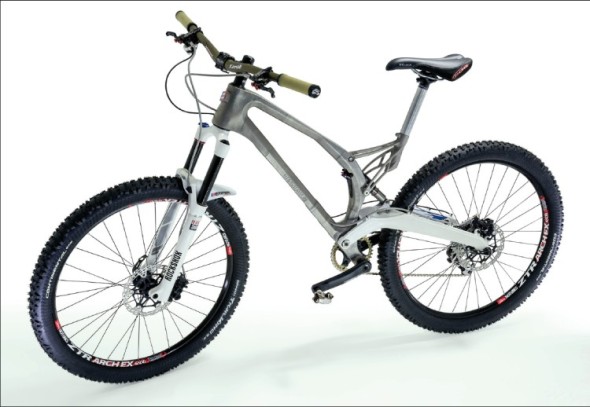
Na konci procesu pak vznikl velmi pevný rám o hmotnosti 1,4 kilogramu, jenž posloužil jako základ celého unikátního horského kola. Standardní hmotnost hliníkového rámu, z něhož se vycházelo, pro představu činila 2,1 kilogramu – to znamená 33% úsporu. Existují kola s ještě nižní hmotností, například karbonová, nicméně jejich životnost podle Chrise Williamse nelze srovnat s rámem kovovým. Aby se vyhnul reklamacím, běžně svoje kola, jež podstupují na kopcích extrémní zátěž, předimenzovává.
Zcela nové možnosti
Náklady na výrobu tohoto unikátního prototypu dosáhly zhruba dvaceti tisíc liber. Není to malá částka, ale hovoříme zde o projektu, který posouvá hranice celého oboru a demonstruje možnosti, o nichž se většině výrobcům dosud možná ani nesnilo. Zásadní úkol – dosáhnout snížení hmotnosti rámu – byl překonán měrou víc než dostatečnou, přičemž vyvstaly zcela nové horizonty, kam se může vývoj kol ubírat.
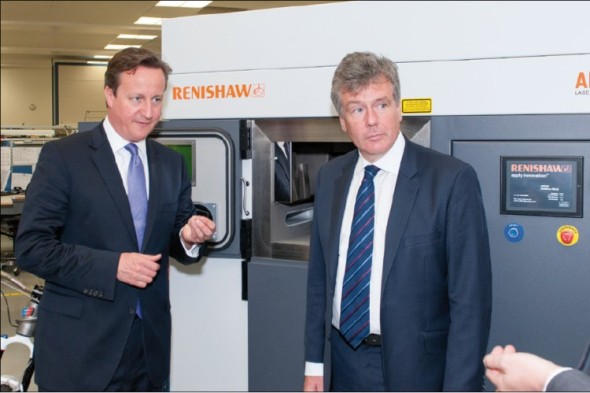
Je to především ohromná svoboda při tvorbě designu a současně maximální skloubení vzhledu a funkce. Použití 3D technologií umožňuje snadno provádět průběžné změny, rychle při vývoji prototypu dosahovat zcela nových objevů a podstatně zkrátit čas od nápadu k produkci komerčního výrobku. Posuzovat nákladovost jedinečného kusu nemá příliš smysl – cena komponentů výrazně klesá v závislosti na sériovosti. Na druhou stranu, aditivní výroba je jedinou volbou tam, kde chcete vyrábět ultralehké a supersilné díly při akceptovatelných nákladech, neboť ty závisejí pouze na objemu použitého materiálu, nikoliv na složitosti výrobků.
Velkou příležitost, vycházející z využití 3D tisku, představuje personalizace výrobků na přání zákazníka. A nejsou to jen emblémy, či sériová čísla vyrobená jako součást rámu – Chris Williams popouští uzdu svojí kreativity a zmiňuje například možnost zabudování RFID čipu přímo do stěny rámu, z níž bude tento bezpečnostní prvek jen velmi obtížně odstranit.
Reklama k nezaplacení
Vedle toho, že se nyní může Empire Bikes chlubit kolem, jaké nikdo jiný nemá a že si jeho tvůrci úspěšně osahali dosud nevyzkoušené možnosti, zafungovalo jeho vytvoření jako velmi efektní PR kampaň, která dalece přesáhla okruh specializovaných cyklistických médií.
S výsledkem spolupráce Empire Bikes a Renishaw se budete moci seznámit osobně na Mezinárodním strojírenském veletrhu v Brně. V rámci výstavy 3D technologií zde bude prezentován titanový rám kola, projektu bude věnována také samostatná přednáška na konferenci „3D tisk – trendy, zkušenosti a obchodní příležitosti“, která se koná v úterý 30. září v pavilonu E brněnského výstaviště.
Pevné a lehké výtisky z titanu
Slitiny titanu mají při zpracování technologií aditivní výroby vysokou mez pevnosti v tahu převyšující 900 MPa a dosahují téměř dokonalé hustoty materiálu převyšující 99,7 %. To je lepší hodnota než při odlévání. Zbytková pórovitost je navíc tvořena malými a sférickými póry, které mají nepatrný vliv na pevnost. Hustota slitin titanu je vyšší než hustota slitin hliníku; relativní hustoty jsou přibližně 4 g/cm3, resp. 3 g/cm3. Proto jediným možným způsobem, jak vyrobit lehkou titanovou verzi hliníkového dílu, je výrazně změnit konstrukci a odebrat materiál, který se nepodílí na celkové pevnosti dílu.
Původní objímka sedlovky ze slitiny hliníku váží 360 g, zatímco odlehčená titanová verze váží 200 g, což je úspora 44 %. To je přitom jen první iterace; další analýzou a testováním by se dala hmotnost snížit ještě více. Původní rám kola váží 2100 g. Po optimalizaci konstrukce pro aditivní technologii klesla hmotnost na 1400 g, což znamená úsporu hmotnosti 33 %.
Testování kompletního rámu bude pokračovat v laboratořích akreditační společnosti Bureau Veritas UK a současně také používáním v horském terénu s monitorováním pomocí přenosných snímačů ve spolupráci s Univerzitou Swansea.
Připravil Jan Homola. Obrazový doprovod poskytla společnost Renishaw.