Česká společnost ProSpon používá s úspěchem již dvanáct let profesionální CAD řešení SolidWorks pro konstrukci speciálních kloubních implantátů a dalších zdravotnických produktů. Společnost zavedla do výroby i 3D tisk kovů z titanové slitiny Ti6Al4V. Zeptali jsme se jejího zástupce Zdeňka Čejky, jak probíhá konstrukční a výrobní proces implantátů.
[Konstruktér.cz] Společnost ProSpon se dostala do povědomí české i světové ortopedické veřejnosti díky výrobě kovových protéz. Můžete popsat, jak probíhá návrh kloubního implantátu a výrobní proces – od přijetí pacienta až po vhojení?
[Zdeněk Čejka, ProSpon] Výrobní, lépe řečeno technologický postup, má svá obecná pravidla. Po vyšetření pacienta na specializovaném pracovišti jsou data ve formě CT dat nebo RTG snímků předána ošetřujícím lékařem do naší firmy. Obsahují již vyznačení resekčních linií a potřebných kotvících prvků (např. šroubů), načež specialista – onkologický konstruktér – vyhotoví první návrh individuálního implantátu vložený do modelu napadené kosti (CT) nebo 2D snímku (RTG). Tento návrh zašle lékaři k odsouhlasení nebo k úpravám. Proces může proběhnout opakovaně a po dokončení návrhu implantátu je stanoven harmonogram výroby v závislosti na operaci pacienta i plánovaném léčení.
Návrh implantátu je vložen do softwaru 3D tiskárny, doplněn o technologické prvky (podpory, výztuhy apod.) a je spuštěn samostatný proces aditivní výroby (3D tisku).
Implantáty jsou v ProSponu vyráběny z titanové slitiny, následně opracovány a potaženy vysoce tvrdou a antialergenní povrchovou vrstvou na bázi uhlíku (metoda povlakování zvaná Diamond-like Carbon Coating – DLC). Tím je implantát hotový a je doplněn o potřebné nástroje na implantaci. Následuje sterilizace a převoz na klinické pracoviště k voperování.
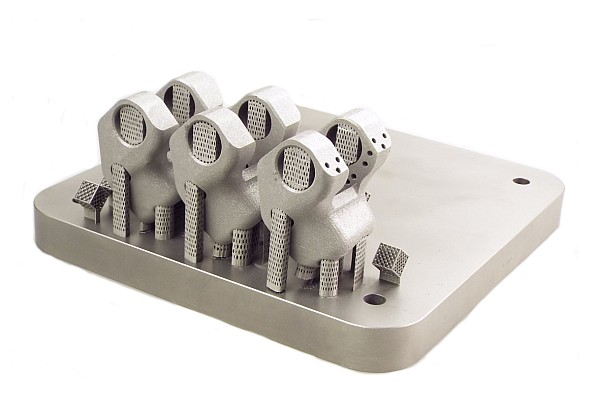
Jak dlouho takový proces trvá, vezmeme-li v úvahu operaci kyčelního kloubu?
Při výrobě jednodušších individuálních implantátů (koleno, kyčel, rameno) je využíván i systém modulárních dílů doplňovaných pouze o individuálně vyráběné části jako jsou kotvící dříky apod. Pak není proces časově náročný a jsme schopni takový implantát vyrobit již za 3 dny.
Jaké znalosti z oblastí medicíny musí mít konstruktér, který implantáty navrhuje?
Kromě standardních strojírenských znalostí o materiálech, technologiích obrábění, povrchových úpravách, konstrukčních softwarech (jako je např. SolidWorks) a podobně, jsou nutnou součástí takovéto práce hodně podrobné znalosti z anatomie a biomechaniky lidských kloubů.
Co je zásadní pro navrhování kloubních implantátů ve vaší společnosti a v čem spočívají výhody profesionálního CAD řešení SolidWorks?
Zásadní jsou zkušenosti, pečlivost, ale i kreativita vývojového pracovníka. V současnosti mají všichni výrobci kloubních implantátů v Evropské unii přibližně stejnou kvalitu svých výrobků na vysoké úrovni. O úspěších návrhů pak rozhodují relativně maličkosti, které odlišují jednotlivé typy. A pokud je konstruktér dokáže vymyslet a zakomponovat do řešení, je to první krok k úspěšnému uvedení na trh. Samozřejmostí musí být zaručená vysoká kvalita v celém řetězci jednotlivých kroků při procesu návrhu, výroby, kontroly i expedice. Chyba v těchto procesech může být fatální pro funkci implantátu a tím by mohlo vzniknout i zdravotní riziko pro pacienta.
Systém profesionálního softwaru SolidWorks s návazností na řízení dokumentace PDM, i softwarový nástroj programování CNC strojů pro výrobu složitých součástí SolidCAM, snižují riziko systémových chyb a samozřejmě umožňují konstruktérovi v krátkém čase potřebný implantát nejen navrhnout, ale i prověřit softwarovou simulací namáhání jednotlivých dílů nebo částí implantátu. I modifikace jednotlivých konstrukčních návrhů (tzv. konfigurace) v SolidWorksu jsou snadné a efektivní a umožňují naplno využít možností jak softwaru, tak i konstruktéra.
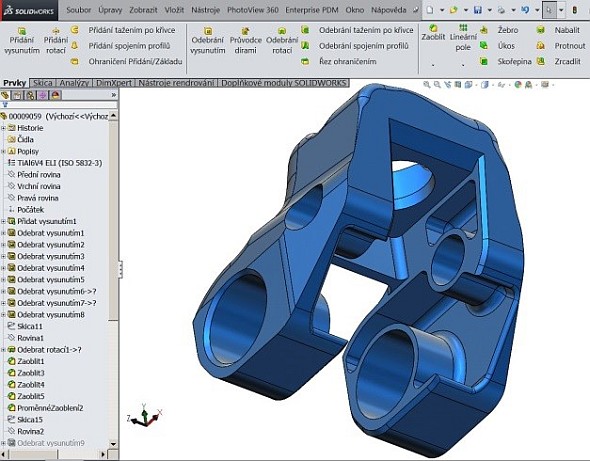
Co bývá nejčastějším rozhodujícím faktorem při navrhování implantátů?
U individuálních implantátů, zvláště onkologických, kterých je většina, je to kromě již zmiňované kvality i rychlost výroby. Mnoho pacientů s agresivními typy nádorů je ohroženo velmi rychlým průběhem své nemoci, a pokud nedojde k adekvátně rychlé reakci i ze strany operatéra, hrozí pacientovi minimálně amputace, ne-li ještě horší následky.
U standardních ortopedických implantátů je ještě kladen důraz na pečlivost a dotažení jednotlivých detailů, protože vývoj takového implantátu trvá i několik let. Je pravděpodobné, že se bude používat i po dobu 10 let a jakékoli opomenutí se projeví buď z hlediska životnosti, nebo i v komfortu operatéra při operaci. To v potenciálním úspěchu (nebo neúspěchu) hraje významnou roli.
Jak je řešena validace a pevnostní analýza implantátů s ohledem na poréznost 3D výtisku?
Samozřejmě, že před prvním použitím 3D tisku na ostrý implantát bylo nutné provést stovky rozborů, pevnostních zkoušek, výpočtů i nastavení parametrů tak, aby byla zaručena jak kvalita, tak i výsledky pevnostní a únavové charakteristiky použitého materiálu. A to jak plné struktury, tak i jednotlivých porézních struktur a jejich vzájemné kombinace.
Jaká zařízení pro 3D tisk kovů používáte a z jakého prášku tisknete?
Využíváme zařízení firmy Concept Laser, jmenovitě se jedná o zařízení M2 Cusing pro laserové spékání kovového prášku. My tento stroj využíváme prozatím na titanovou slitinu Ti6Al4V, která se používá pro výrobu implantátů po celém světě.
Do jaké míry lze snížit hmotnost implantátu 3D tiskem oproti standardním metodám výroby (např. oproti obrábění)?
To není jednoznačné, protože každý typ implantátu vyžaduje jiný přístup. Některé typy implantátů již nelze odlehčit, protože by došlo k zeslabení konstrukce a výhody této technologie se mohou projevit pouze v optimalizaci tvarů nezávislých na možnostech třískového obrábění. Plně však využijí anatomické parametry v místě náhrady. U druhých typů náhrad lze dosáhnout i snížení hmotnosti na 30 %, protože implantát není v celém průřezu nosný a využití porézní struktury je ideální zvláště jako výplň některých velkých defektů.
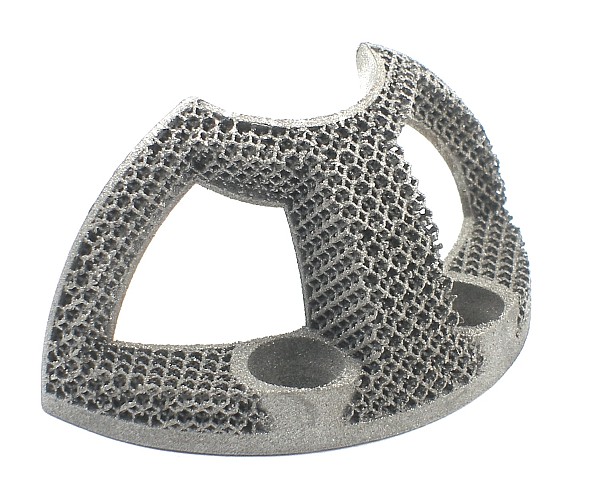
Jak jsou řešeny dokončovací metody a povrchové úpravy?
Dokončovací metody se neliší od dokončovacích metod standardních výrobků. Broušení, leštění, pískování i omílání jsou využitelné v podstatě stejně. Stejně se dají i použít povrchové úpravy jako je anodizování, PVD povlakování, nástřik hydroxyapatitem pro snazší zarůstání apod.
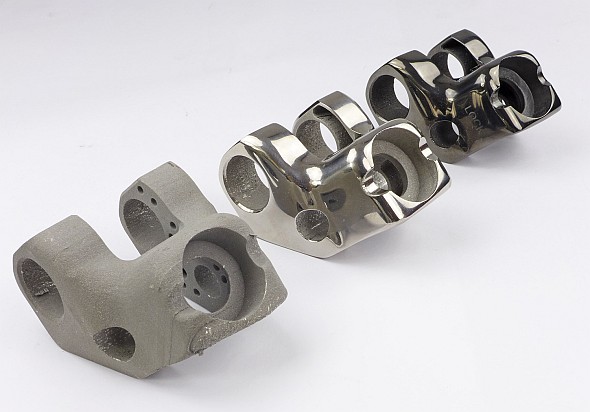
Jaký nejzajímavější a technologicky náročný projekt společnost ProSpon řešila?
Za nejzajímavější v současnosti považuji náš projekt tzv. chytré endoprotézy. Vyvíjíme implantát, který bude minimalizovat rizika spojená s infekcí a to jak po operaci, tak i v průběhu dalšího života pacienta. Je opatřen elektronickým modulem, který v naprogramovaném čase vyhodnocuje několik veličin v okolních tkáních (například teplotu, PH atd.) a po jejich vyhodnocení dá okamžitě signál, že v okolí implantátu vzniká bakteriální infekce. To umožní zasáhnout léčbou včas a ne až po vnějším projevu této infekce, protože to už je na efektivní léčbu většinou pozdě a implantát je nutné reoperovat. Toto řešení jsme si samozřejmě nechali i patentovat, protože zatím žádná firma na světě nic podobného nevyrábí. S tímto projektem jsme uspěli i ve veřejné soutěži ve výzkumu a experimentálním vývoji Program na podporu aplikovaného výzkumu a experimentálního vývoje „ALFA“ Technologické agentury ČR a obdrželi jsme na tento projekt částečnou dotaci.
Co se týká nejobtížnějšího individuálního implantátu, tak je to například totální náhrada celé dolní končetiny včetně kotníku, kolena a kyčelního kloubu pro mladou pacientku ve věku 21 let. Dále se můžeme pochlubit dokončením sacry – náhrady křížové kosti vyplněné porézní strukturou, která se bude operovat pravděpodobně již v únoru.